¿Cómo se puede soldar el acero?
¿Desea soldar piezas de acero? Soldadura MMA, MAG, TIG, Plasma, Arco Submergido, Laser y Oxiacetilenica, Air Liquide le explica los procesos de soldadura posibles para este tipo de metal y cúales le permitirán obtener un resultado de calidad.
Lectura: 6 min
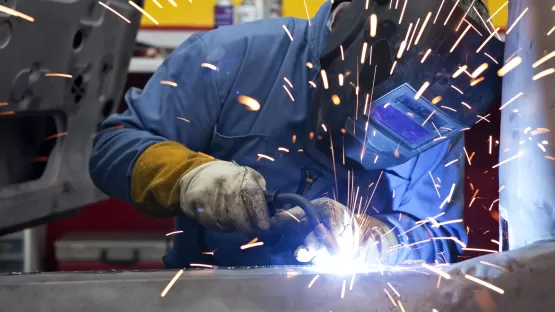
Independientemente del proceso utilizado, la soldadura del acero requiere cuidados especiales y una formación adecuada de los soldadores.
¿Tiene alguna pregunta sobre la soldadura de aceros?
Soldadura MMA (soldadura por arco con electrodo revestido)
La fusión del metal se produce gracias al calor generado por un arco que se establece entre un electrodo revestido y el metal a soldar. Los electrodos se componen de un alma central y un revestimiento, en función del material a soldar y prestaciones buscadas se selecciona el tipo de electrodo y su diámetro.
Como principales ventajas, tenemos:
- Equipo soldeo relativamente sencillo y portátil.
- No necesita aporte adicional, ni transporte de botellas de gas.
- Se puede soldar en lugares abiertos y cerrados.
- Posibilidad de soldar juntas con mal acceso.
- Soldadura en todas las posiciones.
- Aplicable a mayoría de metales y espesores (>2 mm).
Como principales limitaciones, podemos mencionar:
- Proceso lento, por baja tasa de deposición y retirada de escoria.
- Requiere gran habilidad por parte del soldador.
- No aplicable metales bajo punto fusión: Sn, Pb, Zn.
- No aplicable a metales con alta sensibilidad de oxidación: Ti, Nb.
- Baja productividad.
Soldadura MAG
La fusión del metal se produce gracias al calor generado por un arco que se establece entre un electrodo consumible (alambre o hilo de soldadura) y el metal a soldar, bajo una atmósfera de protección de un gas activo (Oxidante).
El proceso MAG es el más utilizado para soldar aceros al carbono acompañados con una mezcla de gases: argón / CO2 o argón / O2. Pero también se pueden utilizar mezclas ternarias de argón / CO2 / O2.
Esta mezcla puede variar en función del tipo de acero a soldar, el espesor, las características estructurales de la unión buscadas, el tipo de hilo utilizado (macizo o tubular) y de las diferentes condiciones de soldadura (manual o automática / robotizada).
Como principales ventajas, tenemos:
- Adecuado para todos los metales.
- Permite soldadura en todas las posiciones.
- Alta tasa de deposición (2 a 6 kg/h las más habituales).
- Soldaduras de gran longitud sin parar.
- Automatizable/robotizable.
- No se genera escoria (excepto en la soldadura del hilo tubular flux core).
- Alta tolerancia al ajuste.
Como principales limitaciones, podemos mencionar:
- Equipo relativamente complejo.
- Mayor nivel de humos que la soldadura TIG.
- Limitaciones de acceso a soldaduras.
- Proyecciones difícilmente evitables.
- Sensible a las corrientes de aire.
Soldadura TIG
La fusión del metal se produce gracias al calor generado por un arco que se establece entre un electrodo no consumible y el metal a soldar, bajo una atmósfera de gas inerte, o ligeramente reductora. Este tipo de soldadura se puede ejecutar con o sin aportación de material.
Para la soldadura TIG se utiliza Ar (ARCAL™ Prime) o mezclas de Ar/He. En el caso que el metal base sea aceros inoxidable austenítico, se puede adicionar hidrógeno (hasta un 7,5 %).
Como principales ventajas, tenemos:
- Arco estable y concentrado.
- Automatizable/robotizable.
- Soldaduras de gran calidad, gracias al control del aporte (si lo hay).
- Sin proyecciones, ni proyecciones, ni ruido. Es un proceso muy limpio.
- Permite soldar en todas las posiciones.
- Proceso idóneo para tener un control de pasada de raíz.
- Equipo relativamente económico.
Como principales limitaciones, hay que referir:
- Baja tasa de deposición.
- Requiere gran habilidad manual, sobre todo si hay aporte.
- No es económico para espesores fuertes.
Normalmente se hace la pasada de raíz con TIG, mientras para las de relleno se utilizan otros procesos de mayor productividad. - Sensible a corrientes de aire.
- Baja tolerancia al ajuste.
Soldadura Plasma
Es un procedimiento de soldadura al arco donde el calor necesario para la fusión es producido por un chorro de plasma muy concentrado (constreñido) y que multiplica el aporte calorífico. Se produce bajo una atmósfera de gas de protección. En este caso a diferencia del TIG, tenemos un gas central que es el que genera el arco eléctrico y un gas anular que lo encapsula.
Como principales ventajas, tenemos:
- Alta calidad y productividad.
- Baja emisión de humos y proyecciones.
- No se genera escoria.
- Gran precisión.
- Menor consumo de tungstenos que la soldadura TIG.
- Aconsejable para cualquier material metálico.
- Generalmente soldadura automática (excepto microplasma).
Como principales limitaciones, podemos mencionar:
- Inversión alta.
- Poca tolerancia al ajuste (menor que el TIG).
- Uso de varios gases (gas arco piloto, gas anular, gas de raíz, gas de protección trasera…).
¿Tiene alguna pregunta sobre la soldadura de aceros?
Soldadura por arco submergido
La fusión del metal se produce gracias al calor generado por un arco que se establece entre el electrodo consumible (hilo) y la chapa, que está protegido por la escoria generada por un fundente, granulado o en polvo y es suministrado a través de una manguera desde el depósito de fundente.
Como principales ventajas, tenemos:
- Es un procedimiento completamente automatizable.
- Permite utilizar altas velocidades de soldadura y de deposición.
- No se producen salpicaduras, ni deslumbramientos debidos al arco, por actuar bajo una capa de Flux.
- Bajo nivel de emisión de humos.
- Los parámetros de soldeo se pueden ajustar perfectamente.
- El enfriamiento lento del cordón evita la aparición de tensiones internas.
- Se puede utilizar en zonas expuestas al viento.
- Alta penetración que permite reducir o eliminar las preparaciones.
- Soldadura sin defectos y de gran productividad (25-45 kg/h).
- La capa de flux impide la radiación y la consiguiente pérdida del calor generado por el arco.
- El flux permite añadir elementos de aleación deseables.
Como principales limitaciones, podemos mencionar:
- No es adecuado para todos los materiales.
- Suele ser necesario empleo respaldo.
- Fundente puede sufrir contaminaciones.
- No aplicable a espesores bajos (por debajo de 3 mm).
- Solo a tope en posición plana y en ángulo (aplicaciones especiales en cornisa).
Soldadura laser
La fuente de energía necesaria para fundir el material base, y el de aportación en el caso de que exista, viene dada por un rayo láser.
Habitualmente, la utilización en la industria de este tipo de soldadura se realizaba en aplicaciones automáticas / robotizadas. Pero en los últimos años se han desarrollado equipos que permiten la soldadura manual sin aportación, o con aportación de hilo automática similar a la de la soldadura MIG/MAG.
Como principales ventajas de la soldadura manual tenemos:
- Aportación de calor muy focalizada, por lo que se reduce la ZAT (zona afectada térmicamente) y las tensiones térmicas introducidas. Esto la convierte en una buena alternativa para la soldadura de aceros galvanizados.
- Requiere menos habilidad por parte del soldador que la soldadura TIG.
- Depende del material a soldar se puede usar argón o nitrógeno como gas de protección.
Como principales limitaciones de la soldadura manual, hay que referir:
- Son necesarios sistemas de seguridad para garantizar la protección de los ojos frente al haz de láser.
- Está limitado a soldadura de chapa fina.
- Tolerancia a la preparación.
Como principales ventajas de la soldadura automática tenemos:
- El láser como luz no tiene inercia, lo que favorece arranques y paradas rápidos.
- Aportación térmica más localizada (alta densidad de energía), consiguiendo mayores velocidades de soldadura, por lo tanto se disminuye la HAZ, las tensiones térmicas y las deformaciones.
- Se puede utilizar a su máximo potencial a presión atmosférica.
- Proporciona cordones estrechos y de gran penetración.
- Proporciona uniones de alta precisión.
- Mayor velocidad de soldadura.
Como principales limitaciones, podemos indicar la tolerancia a la preparación y la inversión.
Soldadura oxiacetilénica
Proceso de soldeo por fusión, dónde la energía necesaria se genera a través de una llama de oxígeno y acetileno. Se puede realizar sin aportación, en cuyo caso hablamos de soldadura autógeno, o con aportación de material mediante una varilla.
La llama oxiacetilénica que se utiliza para soldar:
- Permite que se consiga una temperatura de llama de 3100ºC aproximadamente, y energía necesaria para fundir dichas aleaciones.
- Se caracteriza porque se obtiene una cantidad de elementos reductores suficiente para proteger la unión.
Como principales ventajas, tenemos:
- Equipo de soldeo es de bajo coste, normalmente portátil y muy versátil,
Como principales limitaciones, mencionamos:
- Grandes deformaciones y tensiones térmicas causadas por elevado aporte térmico debido a la baja velocidad de soldeo.
- Lento, de baja productividad y destinado a espesores pequeños.
- Requiere gran habilidad por parte del soldador.
¿Tiene alguna pregunta sobre la soldadura de aceros?
Descubra nuestras soluciones
¿Tiene alguna pregunta sobre la soldadura de aceros? Rellene nuestro formulario de contacto
Nuestros expertos le responderán lo antes posible.Más información
- ¿Qué es la soldadura? ¿Cómo funciona el proceso de soldadura?
- Corte por láser
- Soldadura por plasma
- Corte por plasma
- El proceso de soldadura MIG / MAG (GMAW)
- Pantallas y máscaras para soldadores
- El proceso de oxicorte
- Temperatura de fusión de un metal
- Máquina de soldar
- Metal de aporte en MIG / MAG
- Proceso por arco sumergido
- Antorchas de soldadura
- Soldadura por resistencia
- Soldadura TIG / de metales
- Mezcla de gases para la soldadura por fusión
- Defectos en la soldadura
- El metal de aporte
- Soldadura por arco de plasma
- Proceso de soldadura blanda o fuerte
- Cobre y aleaciones
- Procesos de soldadura
- Soldadura por Arco Eléctrico
- Gas inerte para soldadura
- Seguridad en soldadura
- Soldadura: Argón botella 20L o 50L a 200 bar
- Soldadura por láser
- Soldadura automática
- Procesos de soldadura por gas
- Soldadura MMA
- Posiciones de soldadura
- Soldadura por arco con gas protector
- Tipos de electrodos según el revestimiento
- Soldadura con polvo fundente
- Soldadura con electrodo
- Criterios de selección para electrodos revestidos
- Gases para soldadura por arco
Preguntas frecuentes
- ¿Cómo se puede ajustar el caudal de gas en la soldadura?
- ¿Cuál es la diferencia entre los procesos de soldadura MIG y MAG?
- ¿Cómo soldar acero galvanizado?
- ¿Cómo elegir el gas a utilizar en MIG o MAG?
- ¿Por qué utilizar un hilo tubular?
- ¿Cómo se puede soldar el aluminio?
- ¿Qué impacto tiene la pureza del gas de soldadura y corte?
- ¿Cuáles son los defectos de soldadura más comunes?
- ¿Cómo soldar acero inoxidable?
- ¿Cuál es la diferencia entre la soldadura fuerte y la soldadura blanda?
- ¿Cómo elegir el gas a utilizar en TIG o plasma?
- ¿Cómo evitar el consumo excesivo de gas de soldadura?
- ¿Cómo elegir el gas para soldadura TIG?