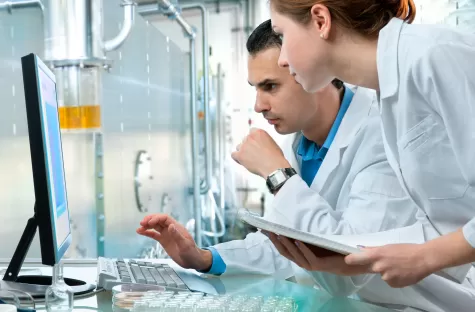
¿Cómo implementar el control de gases en la industria farmacéutica?
Los gases farmacéuticos utilizados durante la fabricación de un medicamento o un principio activo se consideran críticos. Sus cualidades deben estar garantizadas y controladas, desde la fuente de suministro hasta los puntos de uso. ¿Qué controles deben implementarse para asegurar de un modo eficaz el cumplimiento de su calidad inicial?
Principales gases utilizados
Los gases que se controlan más habitualmente en la industria farmacéutica, en particular en la fabricación y acondicionado de fármacos, son el nitrógeno (N2), el aire comprimido, el oxígeno (O2) y el dióxido de carbono (CO2).
La aplicación de los gases para uso farmacéutico o médico se basan en:
- textos y reglamentos rigurosos como la Farmacopea Europea (también las Farmacopeas Japonesa y Estadounidense),
- la norma ISO 8573 relativa al aire comprimido y sus diferentes clases de atmósferas controladas mediante las Buenas Prácticas de Fabricación (BPF).
En estos mismos textos también se especifican los métodos analíticos a implementar.
En términos de control de calidad, los gases farmacéuticos deben cumplir con las especificaciones físicas y químicas descritas en las monografías. Por ejemplo, para la Farmacopea Europea:
- Nitrógeno (N2) n.º1247
- Nitrógeno pobre en oxígeno n.º1685
- Oxígeno (O2) n.º0417
- Dióxido de carbono (CO2) n.º0375
A ese efecto, en estas monografías se describen en detalle los métodos analíticos que se utilizarán.
Ejemplo para el nitrógeno y el control durante la producción:
N2 | Especificación | Técnica analítica |
---|---|---|
Pureza | ≥ 99.5% v/v | Cromatografía de gases GC |
O2 | ≤ 50 ppm v/v | Celda electroquímica |
CO | ≤ 5 ppm v/v | Analizador por infrarrojos |
CO2 | ≤300 ppm v/v | Analizador por infrarrojos |
H2O | ≤ 67 ppm v/v | Higrómetro electrolítico |
Es importante referir que se pueden realizar análisis bacteriológicos o de partículas según la norma ISO 14644-1 u otras especificidades requeridas por el cliente.
Las tres etapas clave en el control de gases farmacéuticos
Los gases farmacéuticos se suministran principalmente a través de proveedores de gas. Tanto si se suministran en forma líquida, que se almacenan en tanques criogénicos, como en forma gaseosa, envasados en botellas o bloques, su calidad se debe controlar en la recepción, así como en diferentes puntos de la(s) red(es) de distribución.
Todas las intervenciones en estas redes (nueva instalación, modificación de un punto, de una ramificación, etc.) requieren la realización de nuevos controles de calidad del gas en los puntos en cuestión antes de la puesta en marcha.
Por lo tanto, hay que considerar 3 etapas clave:
1. La cualificación inicial de la instalación de la fuente de suministro y de la red de distribución antes de la puesta en marcha.
Si el gas suministrado cumple todos los requisitos, es fundamental que la instalación de distribución a los puntos de uso no afecte a la calidad del gas.
Para estar del todo seguros, se puede llevar a cabo una cualificación de la instalación según un protocolo estandarizado:
- A - Cualificación del diseño (DQ, Design Qualification): verificación documentada del cumplimiento del diseño de los sistemas y equipos de gases conforme a los requisitos de la industria farmacéutica y las recomendaciones de los fabricantes.
- B - Cualificación de la instalación (IQ, Installation Qualification): verificación documentada de que los sistemas y equipos están instalados de acuerdo con el proyecto aprobado.
- C - Cualificación operativa (OQ, Operational Qualification): verificación documentada del correcto funcionamiento de las instalaciones, los sistemas y los equipos en cuanto a los diversos parámetros operativos esperados.
- D - Cualificación del rendimiento (PQ, Performance Qualification): verificación documentada de que las instalaciones, los sistemas y los equipos produzcan o mejoren los resultados en consonancia con el rendimiento esperado.
2. El control de los gases en la recepción, en el momento de la entrega, antes de la producción.
Las distintas farmacopeas, el código de salud y las Buenas Prácticas de Fabricación (BPF) exigen la identificación de los gases en el momento de su recepción y la emisión de un certificado de análisis por lote.
La identificación en el momento de la recepción suele ser tediosa y requiere un tiempo en exceso. Para reducir el tiempo dedicado a dicha tarea la unidad de identificación de gases (GIU) de Air Liquide ofrece una solución sencilla y rápida.
Se trata de un proceso que permite tomar muestras de gas de las botellas o de las cisternas en estado líquido, con toda seguridad, antes de su identificación.
Tenga en cuenta que cada fabricante puede implementar una delegación de control y obtener, de su proveedor, un certificado de análisis por lote para cada entrega.
3. El control de los puntos de uso.
Con el fin de proporcionar pruebas de la integridad de los gases industriales hasta los puntos de uso, se debe llevar a cabo una monitorización periódica de la red de distribución.
La planta farmacéutica debe definir una estrategia de control con la realización de análisis. Las pruebas y los análisis pueden ser de tipo físicoquímico, microbiológico y de partículas.
Estas medidas permiten verificar el rendimiento de la red y la ausencia de impacto de ésta en la calidad de los gases, además de velar por los riesgos o problemas de contaminación a lo largo del tiempo.
Las muestras se obtienen en la planta industrial y se rigen por las especificaciones que definen los riesgos, la frecuencia y los métodos de intervención del técnico autorizado, así como los tipos de análisis/pruebas a realizar según el gas y los puntos de muestreo.
Es necesario realizar los análisis mediante obtención de muestras o directamente en línea, en diferentes puntos de la red, desde la fuente hasta los puntos más distantes, teniendo en cuenta también los puntos más críticos del proceso.
Los resultados obtenidos en la planta y en el laboratorio se someten a un tratamiento exhaustivo y se recopilan en un informe completo validado y firmado en el que se especifican los elementos siguientes:
- los métodos utilizados,
- los certificados de conformidad,
- los resultados y los datos brutos,
- los certificados de calibración.
En caso de resultados fuera de especificación, se realizan investigaciones para identificar las causas y las acciones correctivas a implementar. En el control de calidad se pueden registrar los datos transmitidos para hacer un seguimiento de la tendencia con los últimos resultados obtenidos.
En conclusión, después del trabajo o durante el uso, las redes de distribución de gases deben respetar la conformidad e integridad de las características de los gases en el tiempo. Por lo tanto, se requiere un control regular y riguroso.
Quizás le interese...
¿Tiene alguna pregunta sobre el control de los gases farmacéuticos? Rellene nuestro formulario de contacto
Nuestros especialistas le responderán en menos de 24 horasSaber más
Fabricación y conservación de medicamentos
Proteja sus productos e instalaciones con la inertización
Control de la temperatura de una reacción química - ALASKATM
Optimice su proceso de liofilización con frío criogénico
Molienda a temperatura controlada y criomolienda con nitrógeno líquido
Cultivo celular en atmósfera controlada en incubadora, biorreactor o fermentador
Garantice el cumplimiento de las BPF de sus equipos e instalaciones de gases farmacéuticos
Unidad de identificación de gases en la recepción
Atomización por criocristalización de ingredientes con alto contenido en grasas
Nuevos retos para los gases en la fabricación de medicamentos
Inertización con nitrógeno: ¿por qué y cómo se utiliza el nitrógeno en aplicaciones de inertización?
Hacer un buen uso de los gases en I+D y producción biofarmacéutica
Riesgo de incendio y explosiones de gas
¿Cómo se utilizan los gases en el envasado de medicamentos?
Nitrógeno farmacéutico: características y usos
PhargalisTM, la gama de gases y servicios dedicada a la industria farmacéutica y biofarmacéutica
Preguntas frecuentes
¿Cuáles son los diferentes elementos del envasado de medicamentos?
¿Para qué se utilizan los gases farmacéuticos?
¿Cuáles son los principios de la liofilización farmacéutica?
¿Cómo funciona la inertización?
¿Cuáles son las ventajas de tener un analizador de oxígeno en una instalación de inertización?