¿Cuáles son las ventajas del nitrógeno?
La aplicación del nitrógeno (gas inerte) en el proceso de soldadura por ola o de soldadura por refusión tiene muchas ventajas.
Lectura: 3 min
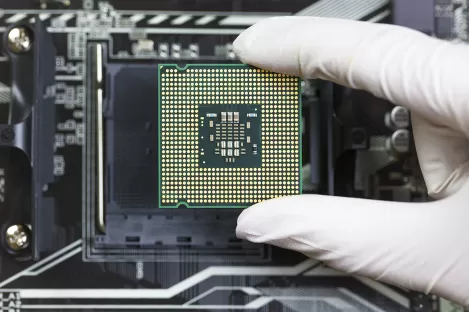
Ventajas del nitrógeno en la soldadura por ola
El uso de nitrógeno en el proceso de montaje de componentes tradicionales PTH en el circuito impreso en una máquina de soldadura por ola, permite, gracias a la reducción del contenido de oxígeno en la atmósfera de soldadura, de:
- ralentizar los fenómenos de oxidación de la aleación,
- aumentar su fluidez,
- y lograr mejor mojado de la aleación a través de los orificios metalizados del circuito impreso.
Los utilizadores del proceso de soldadura por ola en atmósfera inerte de nitrógeno gracias a las propiedades descritas anteriormente benefician de las siguientes ventajas de tipo económico:
- Reducción de la formación de escoria de la aleación.
- Disminución de la cantidad de fundente depositado en los circuitos.
- Reducción del tiempo de limpieza de las olas.
- Reducción de los defectos de las juntas soldadas y mejora de la calidad de la soldadura.
Por todas estas razones, el funcionamiento en atmósfera inerte de nitrógeno es un proceso reconocido por los fabricantes de equipos de soldadura por ola, y todos ellos ofrecen esta solución en su maquinas por defecto sin considerarla una opción.
Ventajas del nitrógeno en la soldadura por refusión
El uso de gas inerte (nitrógeno) en el proceso de montaje de componentes SMD en un horno de refusión reduce del contenido de oxígeno en la atmósfera de soldadura y permite:
- ralentizar el fenómeno de oxidación durante la refusión,
- permitir el uso de placas de soldadura menos activadas en comparación con las utilizadas bajo aire,
- obtener placas más limpias con menos residuos en la superficie,
- obtener juntas de soldadura más fiables, robustas y con buena resistencia mecánica.
Por todos estos motivos, la producción de placas electrónicas en atmósfera inerte es reconocida en este sector como una solución para aumentar la calidad de la soldadura y reducir los defectos de las juntas soldadas. Estos resultados son observables en la etapa de control de las juntas soldadas.
¿Tiene alguna pregunta sobre nuestras soluciones de montaje de componentes electrónicos?
Uso de nitrógeno y seguridad
En materia de seguridad, los sistemas de medición que analisan el contenido de oxígeno del ambiente en el puesto de trabajo son un ejemplo de posibles soluciones para reducir el riesgo de anoxia que se introduce con el uso de gases inertes como el nitrógeno.
De hecho, cuando se inyectan en los equipos, estos gases inertes desplazan o diluyen el oxígeno contenido en el aire de la máquina y su entorno. Si no se evacuan mediante extractores, pueden provocar un déficit de oxígeno, con riesgo de asfixia (anoxia). Por debajo del 18 % de oxígeno en el aire, se pueden sentir los primeros síntomas.
Para protegerse contra los riesgos industriales causados por los gases inertes, le invitamos a que consulte el código laboral o contacte a los expertos de Air Liquide, para saber más sobre las formaciones disponibles sobre la gestión de los riesgos y el uso seguro de lo gases.
¿Conoce la diferencia entre las técnicas de soldadura blanda o fuerte y soldadura?
En el lenguaje común en el ámbito del ensamblaje de placas, a menudo se confunden la soldadura blanda o fuerte y la soldadura.
Una soldadura se obtiene por la fusión de un metal base con un metal de aporte. Las temperaturas elevadas son las que corresponden al punto de fusión de ambos metales. En metalurgia, diferentes tipos de mezclas de gas garantizan la protección de las piezas metálicas soldadas.
Por otro lado, la soldadura blanda o fuerte es un método de ensamblaje que se obtiene fundiendo un metal de aporte (por ejemplo, a base de plata o estaño) sin fundir el metal base. Por lo tanto, el punto de fusión del metal de aporte suele ser una temperatura más baja que la del metal base. La soldadura suele ser llamada blanda cuando la temperatura de fusión del material de aporte es por debajo de 450 °C (como en el montaje de placas) y fuerte por encima de 450 °C.
¿Tiene alguna pregunta sobre nuestras soluciones de montaje de componentes electrónicos?
Nuestras soluciones
¿Tiene alguna pregunta sobre nuestras soluciones de montaje de componentes electrónicos? Rellene el formulario de contacto
Nuestros expertos le responderán lo antes posible.Más información
- Procesos con gas para el ensamblaje electrónico
- Ensamblaje de componentes electrónicos sobre circuito impreso mediante soldadura por ola en atmósfera de nitrógeno
- Soldadura fuerte por refusión en atmósfera de nitrógeno
- Tecnologías de análisis de la fiabilidad electrónica (HALT & HASS)
- Eco Chiller
- Almacenamiento de componentes electrónicos en atmósfera de nitrógeno
- Auditoría y experiencia en el ensamblaje electrónico
- Almacenamiento de componentes en el DryP Cabinet
Preguntas frecuentes
- ¿Cuál es el rol del nitrógeno en la soldadura?
- ¿Por qué almacenar los componentes y tarjetas electrónicas en un almacenamiento seco con nitrógeno?
- ¿Cómo se diseñan las tarjetas electrónicas?
- ¿Cuáles son sus normas de montaje de placas de circuito impreso?
- ¿Cómo se monta un componente en una placa de circuito impreso?
- ¿En qué consiste el proceso de montaje de placas de circuito impreso?
- ¿Cuál es la ventaja de utilizar un intercambiador de calor en mi planta para enfriar el agua de proceso?
- ¿Cuál es el coste del nitrógeno suministrado en forma líquida y producido in situ?
- ¿Cuáles son los peligros del nitrógeno?
- ¿Es fiable el suministro de nitrógeno?