¿Cómo montar un componente en un PCB?
Estas son las principales tecnologías de montaje de componentes en un circuito impreso para la fabricación de placas electrónicas.
Lectura: 3 min
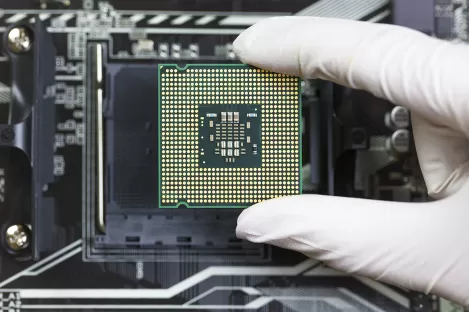
Soldadura manual con soldador
Este es el más antiguo de los procesos de montaje de un componente en un circuito impreso, que además sigue siendo relevante hoy en día para operaciones de cableado, retoque, reparación de componentes pequeños o grandes, tanto si atraviesan la placa como si se montan en su superficie (SMD) (excepto el tipo BGA).
Se lleva a cabo utilizando los siguientes elementos:
- un soldador equipado con un juego de diferentes tipos de puntas,
- un metal de aporte que consiste en un alambre de aleación (esencialmente estaño, cobre y plata) con un fundente de decapado (en el núcleo o en el revestimiento),
- un gas de asistencia para inertizar el extremo de la punta para mejorar la calidad de la soldadura en alternativa a sin gas al aire libre,
- una lupa simple o una lupa binocular para mayor precisión.
El principio consiste en utilizar la transferencia de calor por contacto de la punta con los distintos elementos a soldar. De esta forma, el fundente y la aleación llevados a una determinada temperatura permiten conseguir un mojado tanto en la superficie del circuito impreso, como en la terminación del componente que atraviesa la placa o se monta superficialmente (SMD).
¿Tiene alguna pregunta sobre nuestras soluciones de montaje de componentes electrónicos?
Soldadura por ola
La soldadura por ola se realiza en varias fases de fabricación (caso de un circuito de doble cara):
- La operación comienza con la deposición de varios puntos de cola en la parte inferior del circuito impreso. El siguiente paso es colocar las terminaciones de los componentes montados en superficie (SMD) sobre los puntos de cola. La adhesión entre componentes y circuito impreso se completa con la polimerización en horno.
- La operación continúa con la inserción desde la parte superior del circuito impreso de los componentes que atraviesan la placa (PTH) , que se montan y se bloquean («remachados»). La placa con los componentes SMD pegados en la parte inferior y los componentes PTH insertados en la parte superior estará lista para pasar a la máquina de soldadura por ola.
- El proceso de soldadura a ola empieza con la inyección de un fundente de decapado de óxido en la parte inferior de la placa y en el interior de los orificios metalizados.
- Para reducir los óxidos, este fundente debe someterse a una activación térmica en la zona de precalentamiento de la máquina (calentamiento por resistencias eléctricas).
- La operación finaliza con el paso de la placa por encima de las 2 olas de aleación de la máquina (ola turbulenta y ola laminar) que tocan la parte inferior de la placa para realizar simultáneamente todas las uniones de soldadura. A la salida de la máquina de ola la placa se enfría. Esto es necesario para limitar el estrés y evitar deformaciones de la placa antes de la etapa siguiente que es la prueba funcional.
Soldadura por refusión
La soldadura por refusión se obtiene fundiendo la pasta de soldadura previamente depositada por serigrafía sobre el circuito impreso, entre la superficie de conexión («Pad») y las terminaciones metálicas de los componentes. Esta pasta de soldadura consiste en una aleación de metal a base de estaño, cobre, plata (y otros elementos) en forma de micro esferas en polvo, mezclada con un fundente. Durante el proceso de refusión, se eleva la temperatura de toda la placa, la pasta y los componentes hasta alcanzar el valor de temperatura líquida de la aleación. A esta temperatura, las micro esferas de aleación se funden y se unen entre ellas y comienzan a extenderse para formar la junta de soldadura. Esto corresponde al mojado de la junta de soldadura entre los Pads y en las terminaciones de los componentes. La temperatura sigue aumentando generalmente varias decenas de grados para permitir la refusión de todos los puntos de soldadura y permitir el tiempo suficiente para obtener la perfecta distribución (mojado) del metal sobre las juntas de toda la placa, antes de enfriar el conjunto.
De las medidas para mejorar la calidad del proceso de refusión, el uso de una atmósfera inerte es probablemente una de las más eficaces a la hora de reducir significativamente todos los defectos y retoques.
Unión con colas conductoras
Las colas conductoras son formulaciones a base de resinas sintéticas mezcladas con cargas metálicas. Estas colas aseguran la conductividad de un estrato subtil después de una polimerización realizada a temperatura ambiente o en un horno al aire.
La cola conductora es una solución que se utiliza ocasionalmente para garantizar:
- retoques en las placas ensambladas (para corregir un error de diseño, por ejemplo),
- el establecimiento de conexiones en un conjunto específico: contactos eléctricos entre componentes y un circuito sensible a la temperatura,
- una conexión que requiere un material más blando que la aleación de metal, para resistir la vibración y la deformación.
¿Tiene alguna pregunta sobre nuestras soluciones de montaje de componentes electrónicos?
Nuestras soluciones
¿Tiene alguna pregunta sobre nuestras soluciones de montaje de componentes electrónicos? Rellene el formulario de contacto
Nuestros expertos le responderán lo antes posible.Más información
- Procesos con gas para el ensamblaje electrónico
- Ensamblaje de componentes electrónicos sobre circuito impreso mediante soldadura por ola en atmósfera de nitrógeno
- Soldadura fuerte por refusión en atmósfera de nitrógeno
- Tecnologías de análisis de la fiabilidad electrónica (HALT & HASS)
- Eco Chiller
- Almacenamiento de componentes electrónicos en atmósfera de nitrógeno
- Auditoría y experiencia en el ensamblaje electrónico
- Almacenamiento de componentes en el DryP Cabinet
Preguntas frecuentes
- ¿Cuál es el rol del nitrógeno en la soldadura?
- ¿Por qué almacenar los componentes y tarjetas electrónicas en un almacenamiento seco con nitrógeno?
- ¿Cómo se diseñan las tarjetas electrónicas?
- ¿Cuáles son sus normas de montaje de placas de circuito impreso?
- ¿En qué consiste el proceso de montaje de placas de circuito impreso?
- ¿Cuál es la ventaja de utilizar nitrógeno en la soldadura por ola y en la soldadura por refusión?
- ¿Cuál es la ventaja de utilizar un intercambiador de calor en mi planta para enfriar el agua de proceso?
- ¿Cuál es el coste del nitrógeno suministrado en forma líquida y producido in situ?
- ¿Cuáles son los peligros del nitrógeno?
- ¿Es fiable el suministro de nitrógeno?