Soluciones de Air Liquide para la fundición y el reciclaje de acero y metales no férreos
¿Tiene alguna pregunta sobre la oxicombustión para la industria metalúrgica?
Nuestros expertos pueden ayudarle con su proyecto proponiéndole las soluciones que mejor se adapten a sus necesidades.
¿Por qué elegir las soluciones de Air Liquide?
Air Liquide ofrece tecnologías patentadas de oxicombustión para la industria metalúrgica. Están pensadas en particular para las fundiciones de hierro colado, el reciclaje de acero y el reciclaje de metales no férreos (aluminio, cobre y otros). Incluyen quemadores de oxicombustible con bajas emisiones de óxidos de nitrógeno (NOx) y dispositivos de enriquecimiento de oxígeno para hornos de cubilote y rotativos.
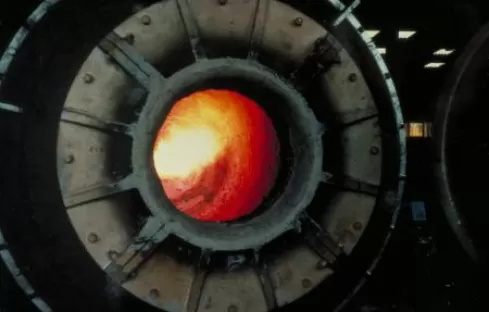
Ventajas de las tecnologías de oxicombustión
Se trata de palancas esenciales en la transición energética, destinadas a reducir las necesidades de energía y las emisiones a la atmósfera derivadas del uso de combustibles fósiles
1. Eficacia superior de la combustión
La sustitución total o parcial del aire de combustión por oxígeno restringe el volumen de nitrógeno térmicamente innecesario para alcanzar los puntos de fusión. Reduce las necesidades de combustible hasta en un 60 %.
2. Reducción de las emisiones atmosféricas
La reducción del consumo de combustibles fósiles se traduce en la correspondiente reducción de las emisiones de CO₂.
El uso de oxígeno puro en la combustión evita la oxidación del nitrógeno a altas temperaturas y reduce las emisiones residuales de óxido de nitrógeno (NOx) en más de un 90%, dependiendo de las entradas de aire parásito en el horno y de la composición de los materiales fundidos.
3. Eficacia operativa
La oxicombustión mejora la transferencia de radiación de calor en los hornos (combustión por etapas, llamas planas, etc.). En comparación con la combustión con aire, los quemadores de oxicombustible permiten que las propiedades de la llama varíen de forma en función de la llama varíen su forma, en función de la duración de los ciclos, dependiendo de si son:
♦ reductoras, para evitar la pérdida de rendimiento debida a la oxidación de las materias primas que se produce a temperaturas de fusión de los metales, u
♦ oxidantes, para quemar los gases combustibles residuales de los gases de combustión.
Una oferta completa
La oferta de Air Liquide está compuesta por dos elementos:
- el suministro de oxígeno con baja huella de carbono,
- y una gama completa de tecnologías de oxicombustión diseñadas para el proceso de fabricación de metal fundido o piezas metálicas.
El amplio soporte continuo de expertos en combustión forma parte de la oferta; desde el diseño del proyecto hasta la puesta en marcha de las instalaciones. También se puede recurrir a especialistas para realizar análisis precisos de riesgos y auditorías de evaluación técnica.
Todos nuestros clientes se benefician de los conocimientos de nuestros especialistas que le darán apoyo para la adecuada aplicación de las diferentes soluciones de oxicombustión (según el tipo de horno, los tipos de materiales a reciclar y los puntos de fusión de los metales y aleaciones).
Para alcanzar los objetivos sectoriales de neutralidad de carbono, y como complemento a la oxicombustión, Air Liquide también ofrece soluciones de captura, transporte y secuestro o reutilización de CO₂ (CCUS) por medios criogénicos o químicos. Estas soluciones consiguen reducir el dióxido de carbono (CO₂) procedente de procesos de combustión industrial.
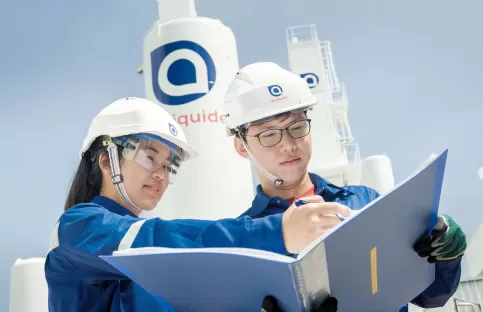
Air Liquide un socio estratégico
Air Liquide es un socio estratégico para muchas empresas metalúrgicas de todo el mundo. El oxígeno es necesario para numerosas aplicaciones en este sector, concretamente en la producción de acero, cobre, aluminio, níquel y zinc. Cuando se consumen grandes volúmenes de gas, el transporte por canalización ofrece una alternativa al transporte marítimo terrestre y al consiguiente impacto medioambiental. Es el sistema de entrega más eficaz y fiable para las grandes empresas. Suministramos decenas de miles de toneladas métricas diarias a través de canalizaciones a nuestros clientes de todo el mundo.
¿Tiene alguna pregunta sobre la oxicombustión para la industria metalúrgica?
Nuestros expertos pueden ayudarle con su proyecto proponiéndole las soluciones que mejor se adapten a sus necesidades.
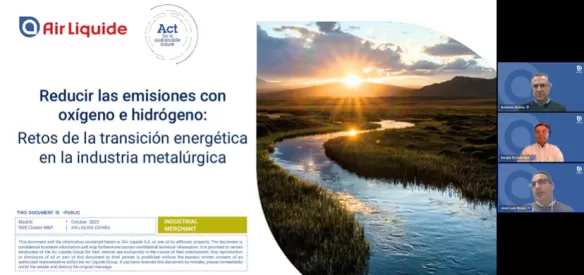
WEBINAR
Reducir las emisiones con oxígeno e hidrógeno. Retos de la transición energética en la industria metalúrgica
¿Quiere saber más sobre el uso y las ventajas del hidrógeno en la combustión o los beneficios que aporta la inyección de oxígeno en los hornos de los procesos de fundición respecto a eficiencia energética, calidad de productos y huella carbónica?
Descubra en nuestro webinar distintos casos prácticos de hidrocombustión y oxicombustión y los resultados logrados con relación al rendimiento y al impacto medioambiental de:
- Aplicación de oxígeno sea para enriquecimiento o sustitución total del aire.
- Inyección de hidrógeno en el combustible.
Testimonio de uno de nuestros expertos en combustión
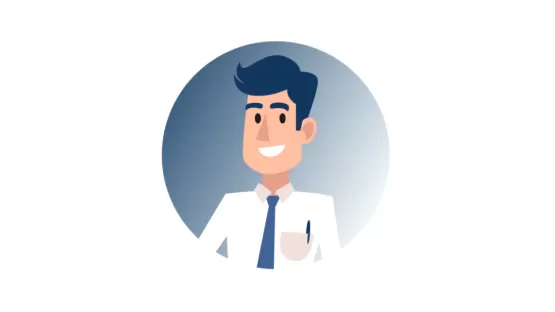
Podemos diseñar y realizar quemadores específicos para un proceso determinado, o adaptar nuestras tecnologías a la configuración de los hornos de nuestros clientes.
Rémi Tsiava, director del Laboratorio Global de Combustión
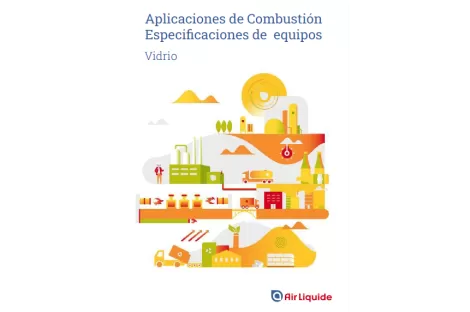
Oferta global
- Oxicombustión para el reciclaje de acero
- Equipos de implementación de la oxicombustión para el reciclaje de acero
- Oxicombustión para el reciclaje de metales no ferreos
- Equipos de implementación de la oxicombustión para el reciclaje de metales no ferreos
- Oxicombustión para fundición
- Equipos de implementación de la oxicombustión para fundición
¿Tiene alguna pregunta sobre la oxicombustión para la industria metalúrgica?
Nuestros expertos pueden ayudarle con su proyecto proponiéndole las soluciones que mejor se adapten a sus necesidades.