Impacto de la oxicombustión en los bloques refractarios de los quemadores
Los materiales refractarios utilizados comúnmente están compuestos de materias primas como óxidos de aluminio (alúmina), circonio y silicio (sílice). Los bloques refractarios fabricados para el aislamiento térmico de los quemadores de oxicombustible son sensibles a los puntos calientes dentro de los hornos de fundición de vidrio.
Lectura: 4 min
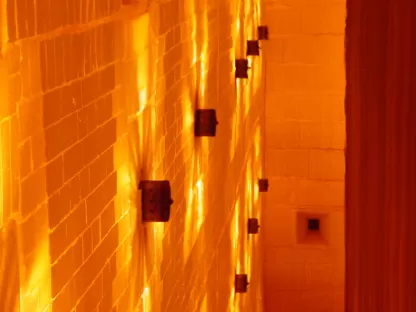
Aunque estén diseñados para resistir a temperaturas muy elevadas, algunas zonas de los elementos refractarios de la superficie de los bloques están expuestas a temperaturas más altas que otras debido a condiciones locales específicas.
Con el objetivo de llevar a cabo mediciones de temperatura, se diseñó un bloque refractario experimental que fue instalado en el horno del centro de investigación que Air Liquide tiene en Francia.
Se instalaron termopares de tipo K de 1,5 mm de diámetro dentro de vainas metálicas fijadas en el material refractario del bloque colocadas a 10 mm de la superficie caliente para evitar condensaciones.
Las temperaturas medidas oscilaron entre 1000 °C y 1300 °C para diferentes potencias térmicas (de 500 a 1500 kW).
¿Necesita asesoramiento sobre la puesta en marcha de la oxicombustión?
La cartografía de temperaturas en el material refractario pone de manifiesto la producción de fuertes gradientes térmicos en la superficie del bloque. La diferencia de temperatura entre el punto más frío y el más caliente es mayor a alta potencia: 150 °C a 1,5 MW frente a 100 °C a 500 kW.
En relación con la posición de la llama, los puntos de fusión más calientes se sitúan especialmente bajo las salidas de gas natural y los más fríos alrededor de los puntos de inyección de oxígeno.
Desde el punto de vista operativo, estos resultados se han utilizado para definir la ubicación de los termopares en los bloques refractarios de los quemadores "online" desarrollados por Air Liquide. El control de la temperatura se utiliza para comprobar la resistencia de los materiales refractarios a la corrosión química. Este fenómeno se debe básicamente a las interacciones con las especies alcalinas presentes en la atmósfera de los hornos de vidrio (potasio, sodio, boro), cuyos efectos pueden degradar la calidad de las propiedades físicas del aislante.
Los quemadores conectados también incluyen sensores de presión, de emisividad de llama y de vibración para controlar su funcionamiento y las intervenciones de mantenimiento preventivo.
Los datos registrados se transmiten por el sistema privado de telecomunicaciones de Air Liquide a una aplicación de Internet de forma a presentar sus valores en tiempo real y enviar alarmas en caso de desviación de los parámetros de funcionamiento.
Con el objetivo de dar apoyo a los proyectos de nuestros clientes, los expertos en procesos de combustión industrial de Air Liquide tienen acceso a esta aplicación para ver los parámetros de los quemadores conectados. En base a ello pueden proporcionar asesoramiento sobre la mejora de sus condiciones de funcionamiento.